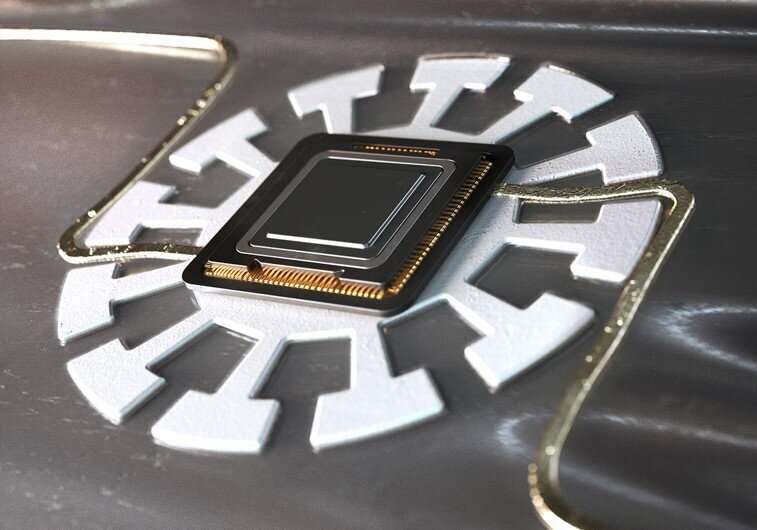
Stretchable electronics can be developed by integrating rigid components in a soft polymer matrix. However, it is challenging to eliminate cracks at the interface between soft and rigid materials. In a new report now published and illustrated on the cover page of Science Advances, Jun Chang Yang, Seungkyu Lee, and a research team in Materials Science, and Mechanical Engineering at the Korea Advanced Institute of Science and Technology in the Republic of Korea, developed geometrically engineered Ferris wheel–shaped islands to effectively suppress crack propagation at the interface under various deformation modes. The optimized shape showed increased strain at failure and fatigue life compared with conventional shapes, including circle and square-shaped islands. The team showed how the electronic skin could differentiate various tactile stimuli without interference while demonstrating notable enhanced durability to withstand conditions of daily use.
Ferris wheel–shaped islands (FWI)
Stretchable electronics allow a variety of hitherto unknown functions by offering various form factors that are usually incompatible with rigid electronics. For instance, stretchable displays, battery packs and logic circuits are vulnerable to lateral strain and can be protected against mechanical deformation via a variety of engineering strategies. However, mechanical mismatch between rigid islands and polymer materials can lead to interfacial cracks and device dysfunction. To solve this, researchers have devised several strategies. In this work, Yang et al presented geometrically engineered rigid islands with excellent mechanical stability at the interface.
Mechanistically, the interlocking structure of the proposed FWI effectively suppressed crack propagation at the interface. The optimized geometrical shapes relied on the mechanical properties of the constituent polymer materials. By design, the repetitive interlocking structure prolonged the fatigue life against various deformation and stretching modes. The team showed a variety of applications of the array, which they developed using Ecoflex polymer material to show stretchable electronics under various deformations and the formation of electronic skin to detect tactile stimuli with durability for daily use with commercial viability.
Developing the FWI embedded in the Ecoflex matrix
Yang et al. used 3D printing to economically manufacture a variety of island shapes. They embedded the printed islands in a polymer matrix, prepared using polylactic acid and Ecoflex, to form an island and polymer, respectively. The FWIs effectively suppressed crack propagation to increase stretchability. The constructs maintained excellent stretchability when compared with various randomly generated shapes. During stretching, to understand crack propagation at the interface, Yang et al used digital image correlation analysis, to obtain the strain distribution of Ecoflex near and on the islands. To derive the FWIs, the team examined the properties of circular shaped islands relative to their stretchability, methods to implement interfacial strength, and the potential to implement mechanical interlocking in the FWIs, to prevent the progression of the cracks via anchored Ecoflex regions.
The researchers 3D printed several different FWIs and analyzed them to confirm the number of “teeth” on the device that were assumed to have the greatest impact on the design, where crack propagation differed for each shape. They developed a finite element simulation method to understand the effect of the island designs on its properties and showed how crack propagation could be regulated between the matrix and the island for FWIs of different material constituents. Yang et al tested three materials, including Dragon skin, Ecoflex, and Ecoflex gel, of which, Ecoflex was best suited to form stretchable electronics.
Mechanical reliability of the constituents and E-skin formation
The scientists noted the effective suppression of crack propagation in the device for enhanced stretchability and prolonged fatigue life of the constructs. They tested the properties via fatigue tests to understand how crack propagation resistance contributed to mechanical stability under a variety of 3D deformations. The results indicated how geometric designs influenced stretchable electronics to propel devices towards a variety of practical applications. The researchers developed the stretchable electronics in the form of an array and encapsulated them with Ecoflex. The construct functioned well across a range of deformation modes for user convenience and durability.
The material can be used for a range of applications, including virtual augmented reality, human-machine interfaces and robotics, under repeated and excessive mechanical deformation. Yang et al used four polypyrrole-coated micropyramidal, polydimethylsiloxane-based piezoresistive pressure sensors on the FWIs, alongside two porous carbon nanotubes and Ecoflex composite-based piezoresistive strain sensors coated on the Ecoflex. They included scanning electron microscopy images and confirmed the appearance of the microstructures. As proof of concept, the team gathered information on daily movements of subjects by using the device to monitor health care via a sensor attached to the knee. Upon attachment, the team decoupled the complex tactile stimuli with simultaneous input of strain and pressure in real-time.
Outlook: Electronic skin
In this way, Jun Chang Yang, Seungkyu Lee, and colleagues developed stretchable electronics for high durability. They engineered FWIs with strong mechanical stability at the interface with accompanying soft polymers. The construct improved strain at failure and prolonged the fatigue life under a range of deformation modes. The FWIs have significant influence on mechanical stability of the substrate depending on the mechanical properties of the polymer constituents. The team used the constructs in practice as stretchable electronics by printing intrinsically stretchable electrodes and placing rigid components on the FWI array, and they developed the electronic-skin to differentiate a variety of physical stimuli. The outcome is applicable for high durability under varying deformation modes, to facilitate the commercialization of electron skins or stretchable electronics in the near future.
Jun Chang Yang et al, Geometrically engineered rigid island array for stretchable electronics capable of withstanding various deformation modes, Science Advances (2022). DOI: 10.1126/sciadv.abn3863
Sihong Wang et al, Skin electronics from scalable fabrication of an intrinsically stretchable transistor array, Nature (2018). DOI: 10.1038/nature25494
© 2022 Science X Network
Citation:
Geometrically engineered rigid island array for stretchable electronics (2022, June 14)
retrieved 14 June 2022
from https://techxplore.com/news/2022-06-geometrically-rigid-island-array-stretchable.html
This document is subject to copyright. Apart from any fair dealing for the purpose of private study or research, no
part may be reproduced without the written permission. The content is provided for information purposes only.
For all the latest Technology News Click Here
For the latest news and updates, follow us on Google News.