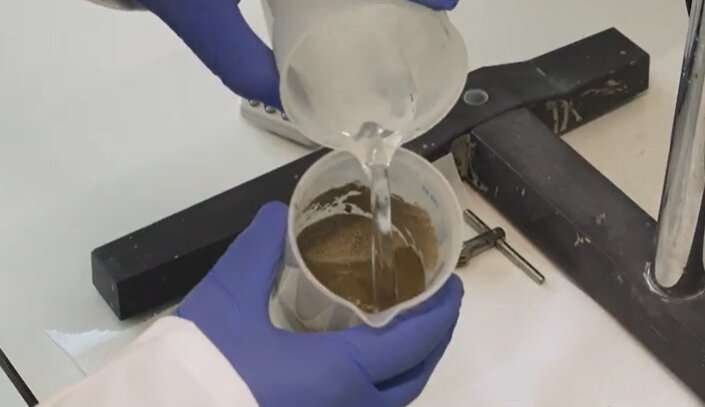
Franco Zunino’s enthusiasm for the object of his research knows no bounds: “The magic and beauty are in the transformation. Concrete starts as a creamy fluid that can be poured into a mold. What emerges is a strong and durable product. This dual nature of concrete enables us to turn even the most far-fetched idea into reality.”
Now round, now angular, concrete structures scrape the sky, break waves and cut through mountains. Concrete provides habitability, and protects against fire, water, pollution and radiation. Combined with steel, this “artificial stone” can withstand huge loads.
“Concrete is a magical material,” says Zunino. No wonder, then, that it continues to proliferate. Humans require ever greater quantities of the stuff, especially in rapidly developing areas of the world such as India, Africa, Southeast Asia and South America. There is, however, a problem: its production consumes an enormous amount of energy and emits large quantities of CO2.
From bakery to kiln
Zunino works in the Physical Chemistry of Building Materials group at ETH Zurich’s Institute for Building Materials. A native of Chile, he has been doing research in Switzerland for six years, as he says, “for the future of our planet.” Since 2022 he has also been supported by an Ambizione grant from the SNSF. Zunino’s grandparents ran a bakery. Today, in the institute’s gleaming laboratory, amid high-performance kilns and mixers, Zunino still recalls the yeasty freshness of Chilean bread. The merest bite catapults him back to his childhood.
As a boy, he was fascinated by the methodical process of baking bread—the precise measuring out of ingredients, the weighing of flour, the reactions in the dough, its consistency and how the flavor developed. “A recipe is all about quantities. A pinch of salt makes bread tasty; too much makes it inedible.” Concrete, too, is refined through minimal amounts of additives. These can make it more workable or fluid, stronger or even more durable. But they can also make it unusable.
Zunino picks up a smooth gray concrete cube. It is made of only a few simple ingredients: cement, sand, gravel, additives and water. Limestone and clay are first heated in a kiln and ground into powder together. The result is cement, a binder that lay people often confuse with actual concrete. Adding water produces a paste that then hardens. Properly formulated concrete is reliable, safe, robust and undemanding—the ideal choice for foundations and columns.
Except for that one problem. The cement-firing process not only consumes energy, but also releases significant amounts of CO2 from the limestone. Consequently, the concrete industry is a major emitter of greenhouse gases and responsible for up to 9% of artificial greenhouse gas emissions worldwide. That corresponds to about four times the contribution of all air traffic. Nonetheless, these figures should be put into perspective.
“Compared to other building materials such as steel, aluminum and glass,” says Zunino, “concrete has a relatively small carbon footprint. The sheer quantity of the material is what makes its footprint seem so immense.” Even timber is an impractical replacement as a building material because far too much of it would be needed: to replace even half of the concrete with timber, you’d probably have to plant a forest the size of India and wait 30 years. “Further improving concrete, this great building material, would be a significant advancement for the industry. The upside is huge.”
For this reason, Zunino and his team want to develop a new family of concrete—ultra-green concrete. The researchers estimate that this could save up to 800 million tons of CO2 worldwide per year, corresponding to 2% of the carbon emissions generated by humans globally or 20 times Switzerland’s carbon emissions.
To achieve this, Zunino will rely on a two-fold strategy. First, the proportion of cement (the particularly CO2-intensive component) will be reduced by around 60%–70% by replacing it with mineral additives. The goal is for these mineral additives, and not the cement, to shape the interactions in the concrete. That will require new types of chemical additives, in particular so-called polymer dispersants, which are a key focus of research. Second, the proportion of binder in concrete—i.e., cement plus water—will also be reduced. The big challenge now is to understand down to the smallest detail the complex balance between flow behavior and strength development so as to retain the same properties despite the changed formulation.
No alternative to concrete
“The human and economic aspects are just as important as the technical ones,” says Zunino. “The material has to cater for everyday demands. If it takes a week to harden, for example, instead of a day or so as is currently the case, it will not find acceptance.”
Thus, the research team is working closely with a large cement manufacturer. “If we are successful, industry will have a solution at hand for meeting CO2 targets and saving on carbon taxes,” he says. Might a completely new building material be a solution? Hardly. “On the streets of Nigeria, where people may sometimes mix concrete with their bare hands, a rocket science solution would have no chance.”
Zunino dreams of having all concrete everywhere replaced overnight by its ultra-sustainable variant, without anyone noticing the difference. He says, laughing: “This would be a transformation as magical as that of the material itself.”
Citation:
Materials scientist working to revolutionize concrete and radically reduce CO2 emissions (2023, April 21)
retrieved 21 April 2023
from https://techxplore.com/news/2023-04-materials-scientist-revolutionize-concrete-radically.html
This document is subject to copyright. Apart from any fair dealing for the purpose of private study or research, no
part may be reproduced without the written permission. The content is provided for information purposes only.
For all the latest Technology News Click Here
For the latest news and updates, follow us on Google News.