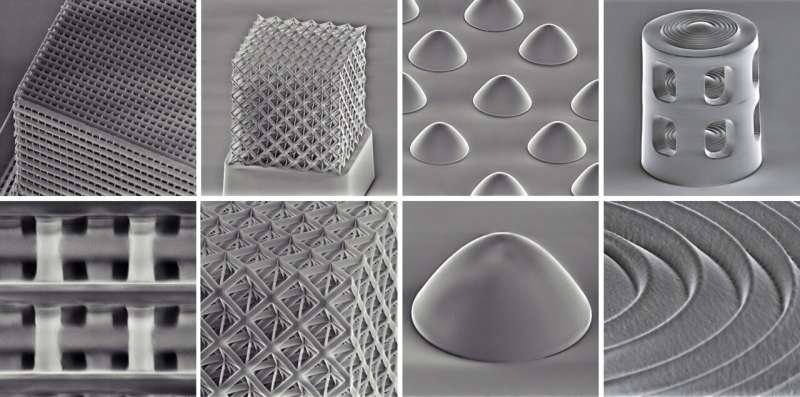
Printing of micro- and nanometer-scaled quartz glass structures from pure silicon dioxide opens up many new applications in optics, photonics, and semiconductor technologies. So far, processes have been based on conventional sintering.
Temperatures required for sintering silicon dioxide nanoparticles are above 1100°C, which is much too hot for direct deposition onto semiconducting chips. A team headed by Dr. Jens Bauer from KIT’s Institute of Nanotechnology (INT) has now developed a new process to produce transparent quartz glass with a high resolution and excellent mechanical properties at far lower temperatures.
Hybrid organic-inorganic polymer resin as feedstock
Bauer, who heads the Emmy Noether Junior Research Group “Nanoarchitected Metamaterials” at KIT, and his colleagues from the University of California, Irvine and the Edwards Lifesciences company in Irvine present the process in Science.
They use a hybrid organic-inorganic polymer resin as the feedstock material. This liquid resin consists of so-called polyhedral oligomeric silsesquioxane (POSS) molecules, which are small cage-like silicon dioxide molecules equipped with organic functional groups.
After cross-linking the material via 3D printing to form a 3D nanostructure, it is heated to 650°C in air to remove the organic components. At the same time, the inorganic POSS cages coalesce and form a continuous quartz glass microstructure or nanostructure. The temperature required for this purpose is only half the temperature needed for processes based on sintering of nanoparticles.
Structures remain stable even under challenging chemical and thermal conditions
“The lower temperature enables the free-form printing of robust, optical-grade glass structures with the resolution needed for visible-light nanophotonics, directly on semiconductor chips,” Bauer explains. Apart from an excellent optical quality, the quartz glass produced has excellent mechanical properties and can be processed easily.
The researchers from Karlsruhe and Irvine used the POSS resin to print various nanostructures, including photonic crystals of free-standing, 97 nm wide beams, parabolic microlenses, and a multi-lens micro objective with nanostructured elements. “Our process produces structures that remain stable even under harsh chemical or thermal conditions,” Bauer says.
More information:
J. Bauer et al, A sinterless, low-temperature route to 3D print nanoscale optical-grade glass, Science (2023). DOI: 10.1126/science.abq3037
Citation:
Nanomaterials: 3D printing of glass without sintering (2023, June 18)
retrieved 20 June 2023
from https://techxplore.com/news/2023-06-nanomaterials-3d-glass-sintering.html
This document is subject to copyright. Apart from any fair dealing for the purpose of private study or research, no
part may be reproduced without the written permission. The content is provided for information purposes only.
For all the latest Technology News Click Here
For the latest news and updates, follow us on Google News.