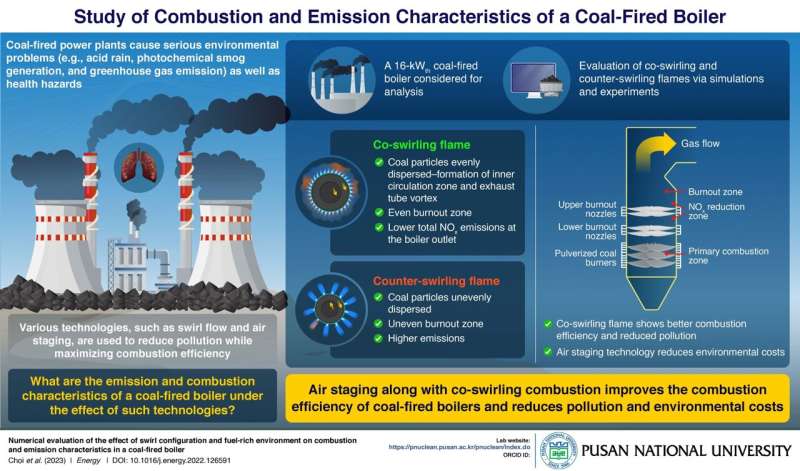
Coal-fired power plants have been in place for a long time to meet the global demands for power generation. Needless to say, there are environmental and human health concerns to be addressed on this front. While there are ongoing efforts to transition to renewable energy resources, coal-fired power plants may not become obsolete just yet.
Against this backdrop, it is pertinent to explore how the efficiency of these coal-fired boilers can be improved while mitigating their harmful effects on the environment, namely greenhouse gas emissions, acid rain, and photochemical smog generation, and the human health.
To this end, various combustion methods like air staging and swirl flow have been proposed. However, the efficacy of these technologies in mitigating the pollutant emissions while maximizing the burnout performance has remained unclear. Now, in a recent study in the journal Energy , an international team of researchers led by Prof. Gyungmin Choi of Pusan National University, Korea analyzed the effectiveness of combining swirl flow and air staging in improving the combustion performance and reducing pollution.
“The exhaust tube vortex (ETV) structure accompanying the swirl flow improves flame stability and combustion performance, but has the disadvantage of generating a large amount of NOx emissions. In contrast, air staging technology creates a fuel-rich environment in the primary combustion zone, which has a positive effect on NOx reduction but negatively affects combustion performance,” explains Prof. Choi. “Therefore, if these two technologies are appropriately combined and applied in real life, a synergistic effect that reduces the emission of air pollutants as well as improves combustion performance can be expected.”
Accordingly, the team employed both simulations and experiments to study the combined effects of different swirl configurations and air staging within a 16-kWth retrofitted down-fired pulverized coal boiler. The coal boiler was composed of three sections: the swirl burner, the boiler, and the exhaust pipe.
For staged combustion, staged air was divided into two sides and injected tangentially into the boiler. Liquified petroleum (LPG) gas was used for preheating and flame stabilization. The staged-air and LPG flow rates were regulated, and for each setting, the temperature was measured using thermocouples. Additionally, the amount of gas-phase species was measured using a multi-gas analyzer.
Air staging with two swirl configurations, namely co-swirling and counter-swirling flames, were evaluated to understand which of these is more beneficial in terms of reducing pollutant emissions. In the case of the co-swirling burner, where the air and fuel circulated in the same sense, the coal particles were evenly distributed owing to the formation of inner circulation zone and the ETV–two vital features for optimizing the design of coal-fired boilers.
Further, the team observed an even burnout zone for the co-swirling configuration, which ensured complete combustion of the fuel, reducing the gas species emissions. It also facilitated an increased conversion of chemical energy into thermal energy, boosting the combustion efficiency. In contrast, counter-swirling burners showed uneven coal particle distribution, uneven burnout, and increased NOx emissions, suggesting that a co-swirling configuration was the better option.
Additionally, the team showed that air staging technology reduced the environmental costs from $0.003 to $0.015 per day.
Overall, the insights from this study could prove to be extremely valuable in solving the environmental problems and health hazards related to coal-fired power plants. “We have identified and studied the structure and flame of the ETV for the first time, and will continue researching and striving to utilize it in the combustion-based industry,” concludes Prof. Choi.
More information:
Minsung Choi et al, Numerical evaluation of the effect of swirl configuration and fuel-rich environment on combustion and emission characteristics in a coal-fired boiler, Energy (2022). DOI: 10.1016/j.energy.2022.126591
Provided by
Pusan National University
Citation:
Researchers examine combined effects of two combustion technologies on the emission of coal-fired boilers (2023, March 16)
retrieved 16 March 2023
from https://techxplore.com/news/2023-03-combined-effects-combustion-technologies-emission.html
This document is subject to copyright. Apart from any fair dealing for the purpose of private study or research, no
part may be reproduced without the written permission. The content is provided for information purposes only.
For all the latest Technology News Click Here
For the latest news and updates, follow us on Google News.